1896
The factory was founded in 1896 as the Machine Factory of the Royal Hungarian State Railways Boiler Manufacturing Plant. After the closing of the Millennium Exhibition in 1896, the factory bought the exhibition pavilion, which was converted into a production workshop and warehouse buildings.
The main machine of the plant was a 600-ton hydraulic press, served by a 5-ton crane and two ovens heated with mazout.
From the beginning of the century, this factory produced the fitting walls of locomotive sheds, boiler bottoms, parts for wagon bogies required for locomotive production and other hot pressed hard sheet parts.
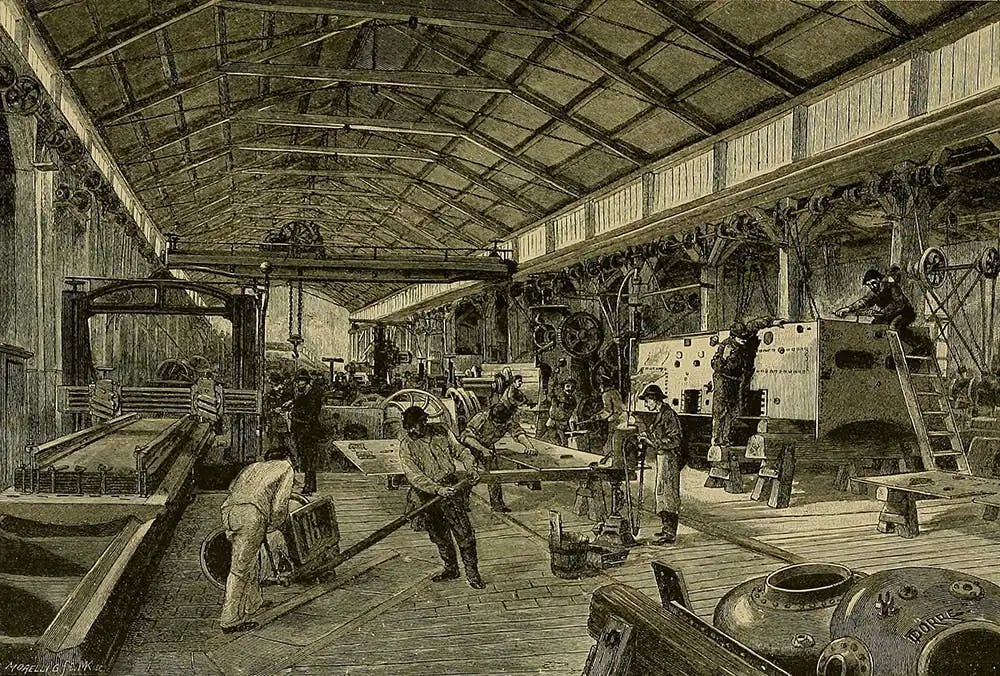
1913
A 2,000-ton water-hydraulic press was ordered, the primary of which its task, in preparation for World War I, was to press the gun bases.
At the same time, the wooden building was also rebuilt, with the aim of incorporating a heavy-duty tall crane.
According to the production reports of the time, 28 tons pressed sheet were produced in 1896 and 1897, 48 tons in 1898, and 93 tons in 1899.
The plant belonged to the Mávag Locomotive and Machinery Factory. Its main profile was pressing of the part walls of the steam locomotive.
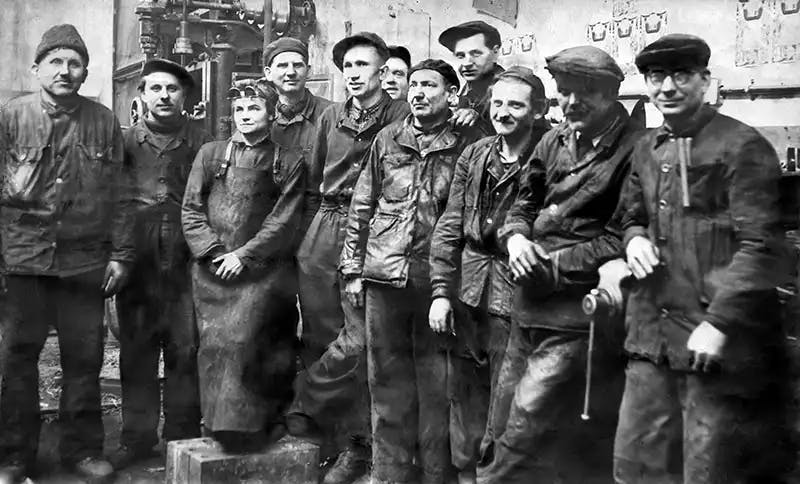
1959
On January 1, 1959, the plant became part of the Ganz-Mávag Locomotive, Wagon- and Machine Factory, with the merger of the Ganz Wagon- and Machine Works and the Mávag Locomotive- and Machine Works.
The main profile changed slowly.
Air spring mounts and bumpers for Ikarus buses and pressed products (for example T56 tank parts) for military industry are also got in the product range.
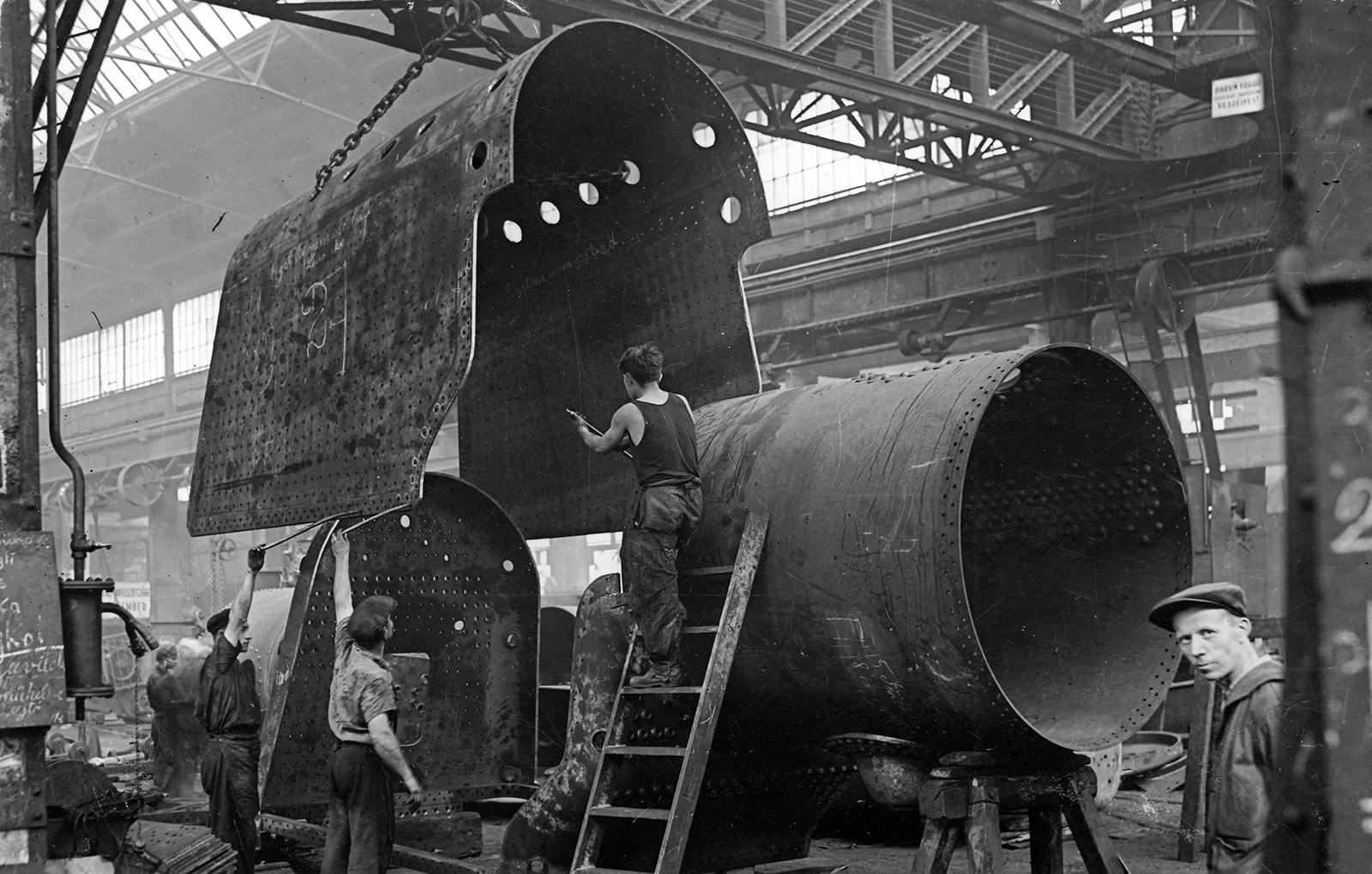
1989
Since Ganz Mávag only produced for Russian and other KGST markets, the company's market collapsed at the same time as the regime change.
After losing markets, the factory declared bankruptcy. They were attempts to continue operating the factory giant by dividing it into smaller plants, but these were unsuccessful, so the liquidation began.
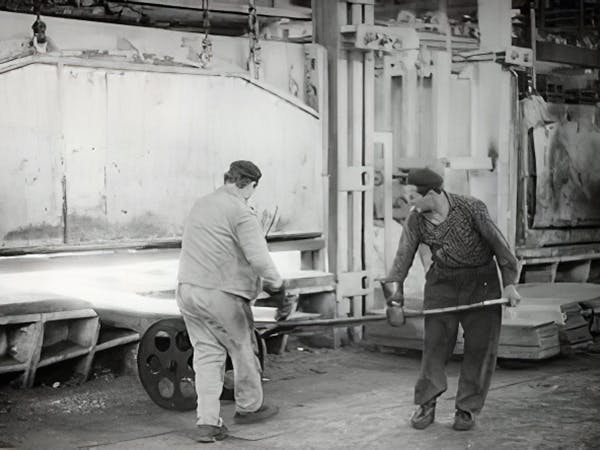
1991
The plant was privatized by a group of Hungarian private owners and started operating under the name Technokov Kft.
Tank bottoms played a more important role in the product range, but the beginning was not easy, because the company had almost exclusively vessel bottom tools according to the MSZ standard, which at that time were still suitable for Hungarian market’s requirements, but the export markets demanded products according to DIN and ASME standards.
The Hungarian tank manufacturers also wanted to sell to foreign markets, so the MSZ standard product was no longer suitable for them either.
Tool transformations began, as a result of which deliveries to the German market began already in the second half of the year.
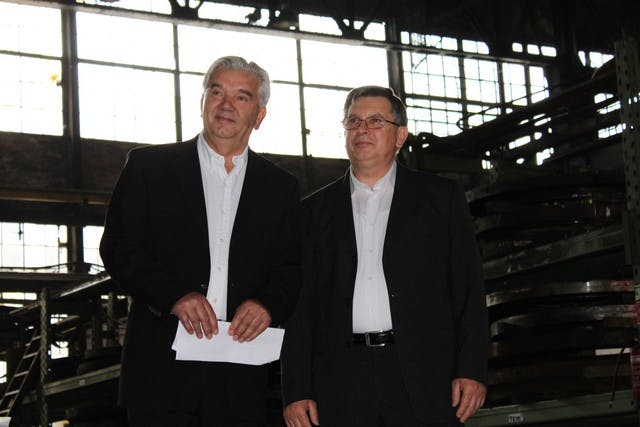
2005
Important investments were made.
The export markets indicated a significant demand for gas tank bottoms, so a 1,000 ton semi-automatic hydraulic press and two lathes with a carousel were purchased for edge processing of the vessel bottoms.
There was also a serious demand for large bottoms in small quantities.
To meet these needs, a Boldrini cold-forming machine line was purchased, with which the maximum production diameter increased from 3172 to 4500 mm.
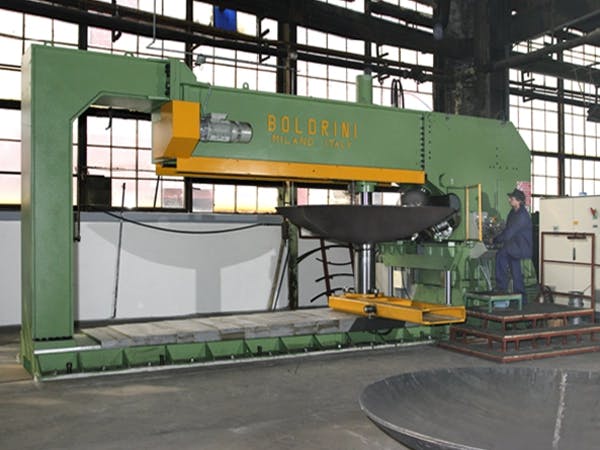
2008
The Company entered the market of railway tank bottoms.
This market segment started with the production of 4 shallow dish bottoms with a diameter of 2900 mm.
Today, the number of railway tank bottoms of various diameters exceeds 2,000 pieces, making this market segment one of the company's strongest "legs".
Of course, this could not be realized without investments..
We needed a conveyor belt sandblaster and two grinding machines.
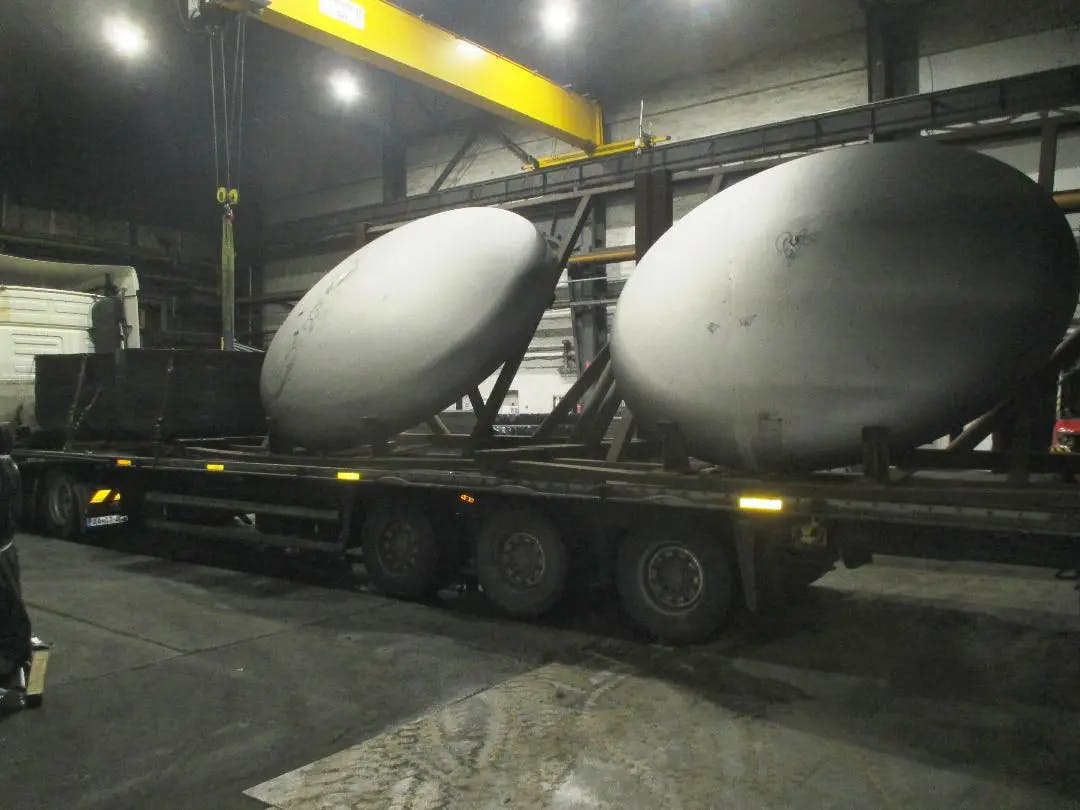
In these days
The search for new market needs and the implementation of the investments necessary to satisfy them is continuous.
In this way, an edge processing machine with new robotic technology, a laser cutting machine, a 3D plasma cutting machine and a tunnel shot blasting machine were purchased.
Today, we deliver to 22 countries, as a result of which our export ratio exceeds 70% and we use more than 10,000 tons of plate compared to the 93 tons of plate used in 1899.
Our principle: "We do everything to ensure that our customers are successful, because then we can be successful too."